Comprehending What is Porosity in Welding: Reasons and Solutions
Porosity in Welding: Identifying Common Issues and Implementing Ideal Practices for Prevention
Porosity in welding is a pervasive issue that typically goes undetected until it creates substantial problems with the honesty of welds. In this conversation, we will certainly check out the vital aspects contributing to porosity development, analyze its damaging impacts on weld efficiency, and discuss the ideal methods that can be embraced to reduce porosity occurrence in welding procedures.
Typical Reasons For Porosity
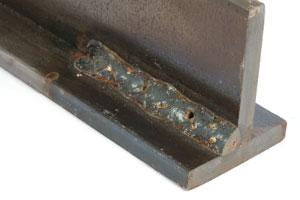
Utilizing filthy or damp filler products can present contaminations right into the weld, adding to porosity concerns. To alleviate these common causes of porosity, comprehensive cleansing of base steels, proper securing gas option, and adherence to optimum welding parameters are essential practices in attaining top quality, porosity-free welds.
Effect of Porosity on Weld Quality

The existence of porosity in welding can substantially endanger the architectural stability and mechanical buildings of bonded joints. Porosity develops gaps within the weld steel, deteriorating its general toughness and load-bearing capacity.
Welds with high porosity levels tend to show lower influence stamina and lowered ability to deform plastically before fracturing. Porosity can restrain the weld's capacity to successfully transfer forces, leading to premature weld failure and potential safety hazards in important frameworks.
Best Practices for Porosity Prevention
To boost the structural integrity and high quality of welded joints, what specific steps can be carried out to decrease the event of porosity throughout the welding process? Porosity avoidance in welding is important to guarantee the honesty and stamina of the last weld. One efficient method is proper cleaning of the base steel, removing any kind of pollutants such as corrosion, oil, paint, or wetness that could bring about gas entrapment. Making sure that the welding equipment is in excellent problem, with clean consumables and proper gas flow prices, can likewise considerably reduce porosity. Additionally, keeping a stable arc and regulating the welding parameters, such as voltage, present, and travel rate, aids produce a constant weld pool that minimizes the threat of gas entrapment. Making use of the appropriate welding strategy for the particular product being welded, such as changing the welding angle and gun placement, can better stop porosity. Regular inspection of welds and prompt removal of any problems recognized during the welding process are crucial practices to stop porosity and create high-quality welds.
Significance of Appropriate Welding Strategies
Executing proper welding methods is extremely important in making certain the structural honesty and quality of bonded joints, building on the structure of reliable porosity prevention procedures. Welding methods straight affect the general strength and resilience of the welded structure. One vital facet of appropriate welding methods is maintaining the appropriate warmth input. Extreme warmth can result in increased porosity as a result of the entrapment of gases in the weld pool. Alternatively, insufficient warm may lead to incomplete blend, developing potential powerlessness in the joint. Additionally, using the ideal welding specifications, such as voltage, existing, and take a trip speed, is critical for achieving audio welds with minimal porosity.
Additionally, the choice of welding process, whether it be MIG, TIG, or stick welding, ought great site to align with the specific requirements of the job to guarantee optimum outcomes. Proper cleaning and preparation of the base metal, in addition to choosing the ideal filler product, are additionally necessary parts of proficient welding techniques. By sticking to these ideal methods, welders can decrease the threat of porosity development and generate high-grade, structurally audio welds.

Testing and High Quality Control Actions
Checking procedures are crucial to detect and prevent porosity in welding, guaranteeing the strength and resilience of the final product. Non-destructive why not look here screening approaches such as ultrasonic screening, radiographic screening, and aesthetic evaluation are generally employed to determine prospective problems like porosity.
Carrying out pre-weld and post-weld inspections is also essential in preserving quality control criteria. Pre-weld evaluations involve validating the materials, tools setups, and sanitation of the workspace to avoid contamination. Post-weld inspections, on the various other hand, evaluate the last weld for any type of issues, including porosity, and confirm that it satisfies defined requirements. Implementing a detailed quality control strategy that includes extensive testing procedures and inspections is extremely important to reducing porosity concerns and guaranteeing the general top quality of bonded joints.
Verdict
Finally, porosity in welding can be a typical issue that influences the quality of welds. By recognizing the typical reasons for porosity and carrying out ideal techniques for avoidance, such as correct welding methods and screening measures, welders can make certain high quality and reliable welds. It is important original site to focus on prevention approaches to reduce the event of porosity and maintain the stability of welded structures.